For now, it's a largely empty brick warehouse in Globeville.
Developer partners Jeff Hopfenbeck and David Schultz imagine it as a factory churning out the parts for sleekly designed homes they will truck in flat packs for assembly wherever affordable homes are needed. And where aren't they?
Yes, they're talking pre-fab homes. Schultz, a builder and son of a custom builder, knows that when some people hear that, they think "double-wide."
A Saab is more what is envisioned by Schultz and Hopfenbeck, who has worked for the international management consulting firm McKinsey & Company.
"Or maybe a Volvo, because Saabs no longer exists," Hopfenbeck said and laughed, adding he has an old Saab he loves.
What they're getting at is that if consumers covet precisely engineered goods such as cars made on assembly lines under strict quality controls, why not homes? Sweden -- which gave the world the Saab as well as the Volvo -- has for decades been a leading manufacturer and consumer of prefab homes. The country was a source of inspiration for Hopfenbeck and Schultz when they founded their Simple Homes company in January.
Sweden "is a working case study for how to build well," Hopfenbeck said.
Their architect John Schwarz traveled to Sweden and saw design that's "simple. It's clean. It's beautiful. It's efficient."
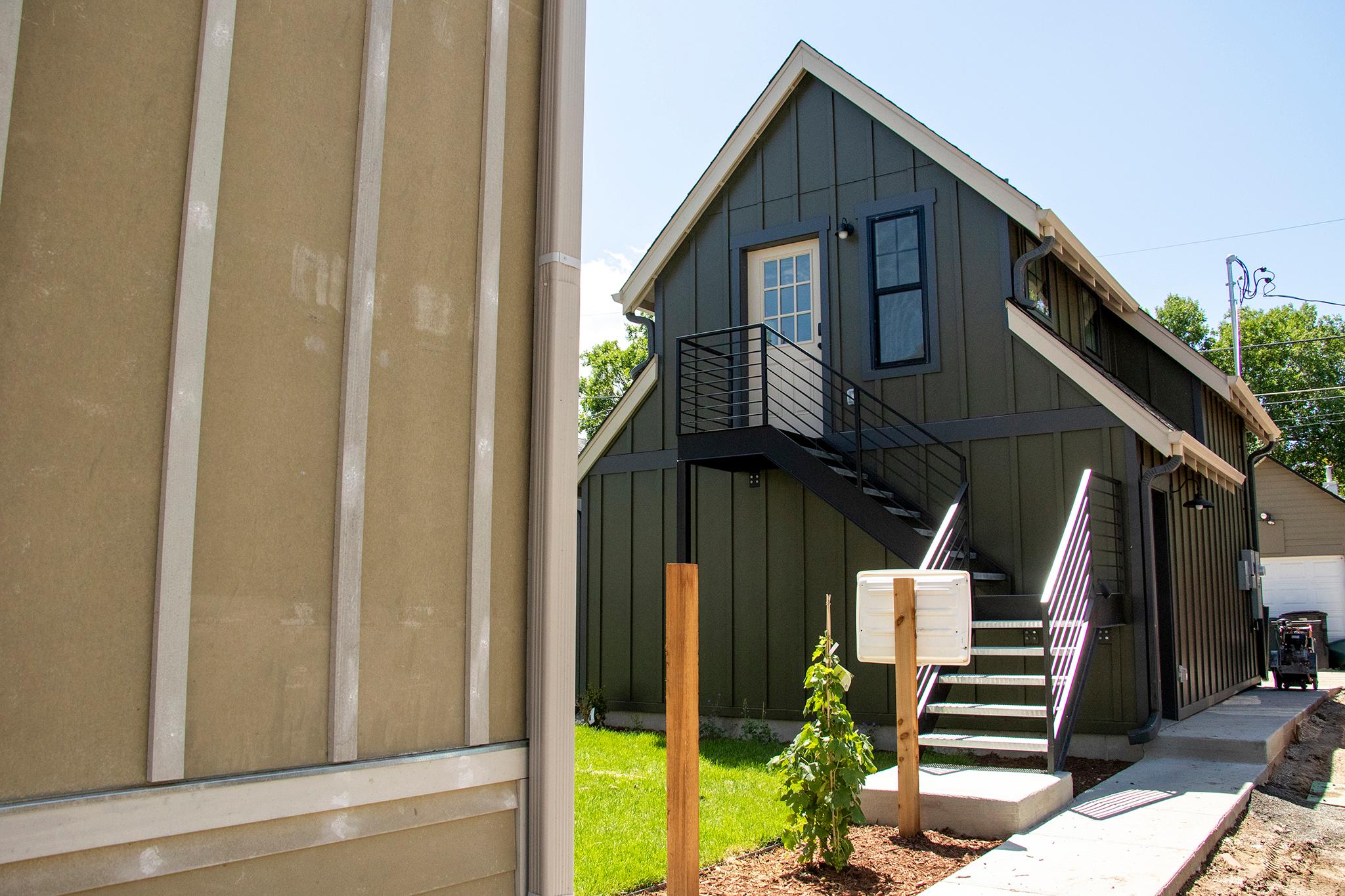
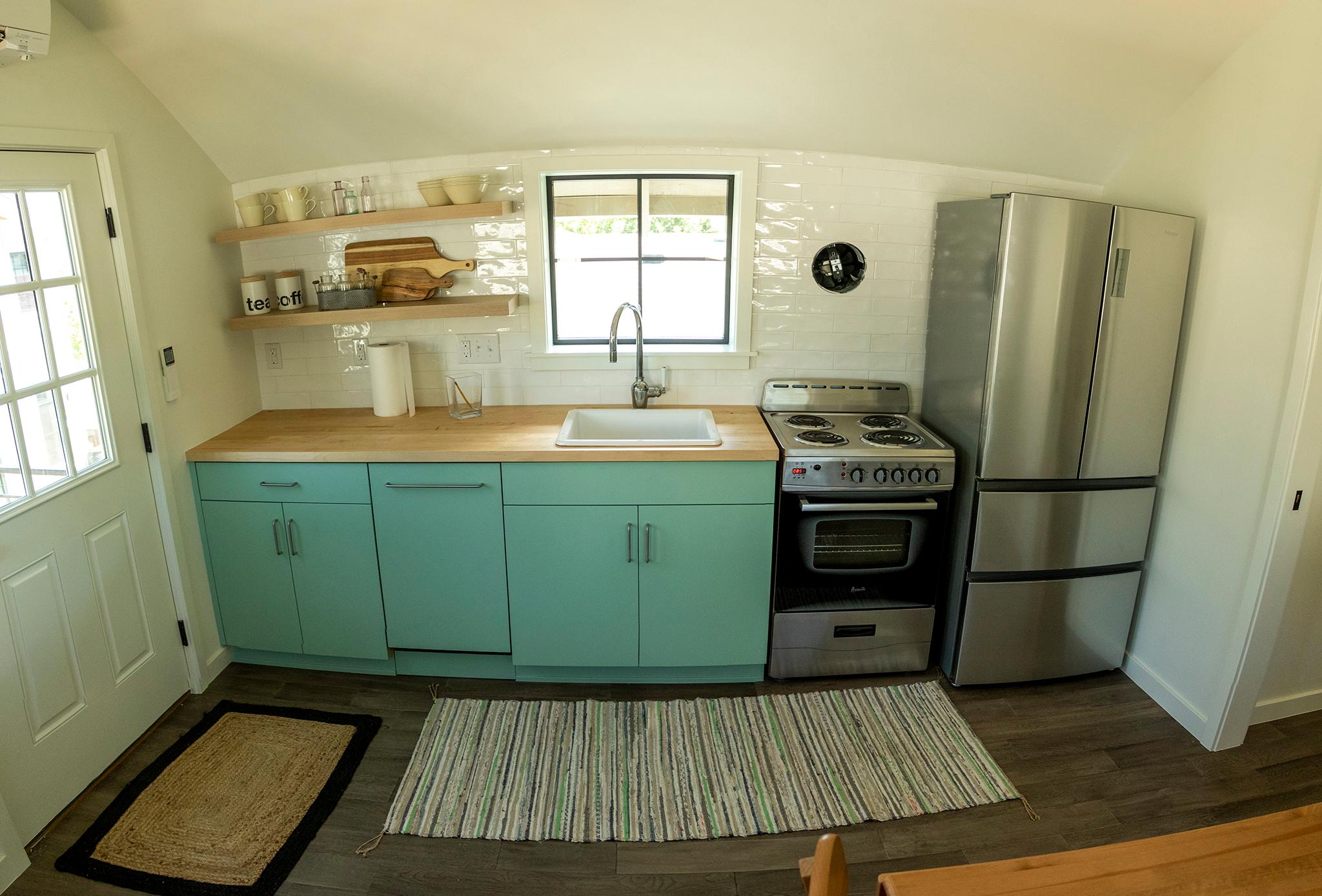
Last month Simple Homes opened its 20,000-square-foot factory in what had been built as a railroad maintenance facility in the 1920s. The headquarters has a lot of the no-nonsense aesthetics Schwarz described. When it's up and running, the Simple Homes team hopes to produce up to 150 single-family homes a year out of Globeville.
Manufacturing will never have to stop because of poor weather, even more of a concern in Sweden than in Colorado. All the work will be done on waist-high platforms, with no need for climbing on dangerous ladders and therefore less risk of injury. In an era when shortages of skilled workers are creating headaches in the construction industry, Simple Homes expects to employ just 20 people at its factory. Most will be designers and engineers working on computers. A half dozen will be building on the factory floor. Hopfenbeck and Schultz said the builders would be able to learn the skills they need fairly quickly on the job.
The factory will be equipped with European technology that includes computer-controlled saws and a laser system that projects blueprints onto the tables where workers assemble panels that will become homes. The whole process will be photographed.
"If there is a defective window, we can go back and say, 'It wasn't detailed right,'" Schultz said.
While waiting for the high-tech equipment, Hopfenbeck, Schultz and a few carpenters assembled their prototype on a platform that Schultz's father helped them build in the Globeville factory. The first Simple Homes home is an accessory dwelling unit, or ADU, also sometimes called a granny flaf. It's a structure in which Schultz's L&D Construction specializes. The unit, which he could rent out for extra income, is in the backyard of a West Colfax home where Schultz plans to move soon with his family.
"We don't have enough of this for single people, couples, elderly people trying to age in place," Schultz said of his 320-square-foot prototype.
He projected that 20 percent of the construction costs could be saved by producing most of a home on the factory floor instead of at a site. That still leaves land and other costs, but it's a start.
While working at McKinsey, Hopfenbeck was introduced to how robotics and automation were rewriting the future of many fields. But not construction, at least not in the United States, where he saw possibilities for addressing the housing crisis with more efficient and cost-effective methods.
"I've just always been frustrated by the way we build homes in the U.S." Hopfenbeck said.
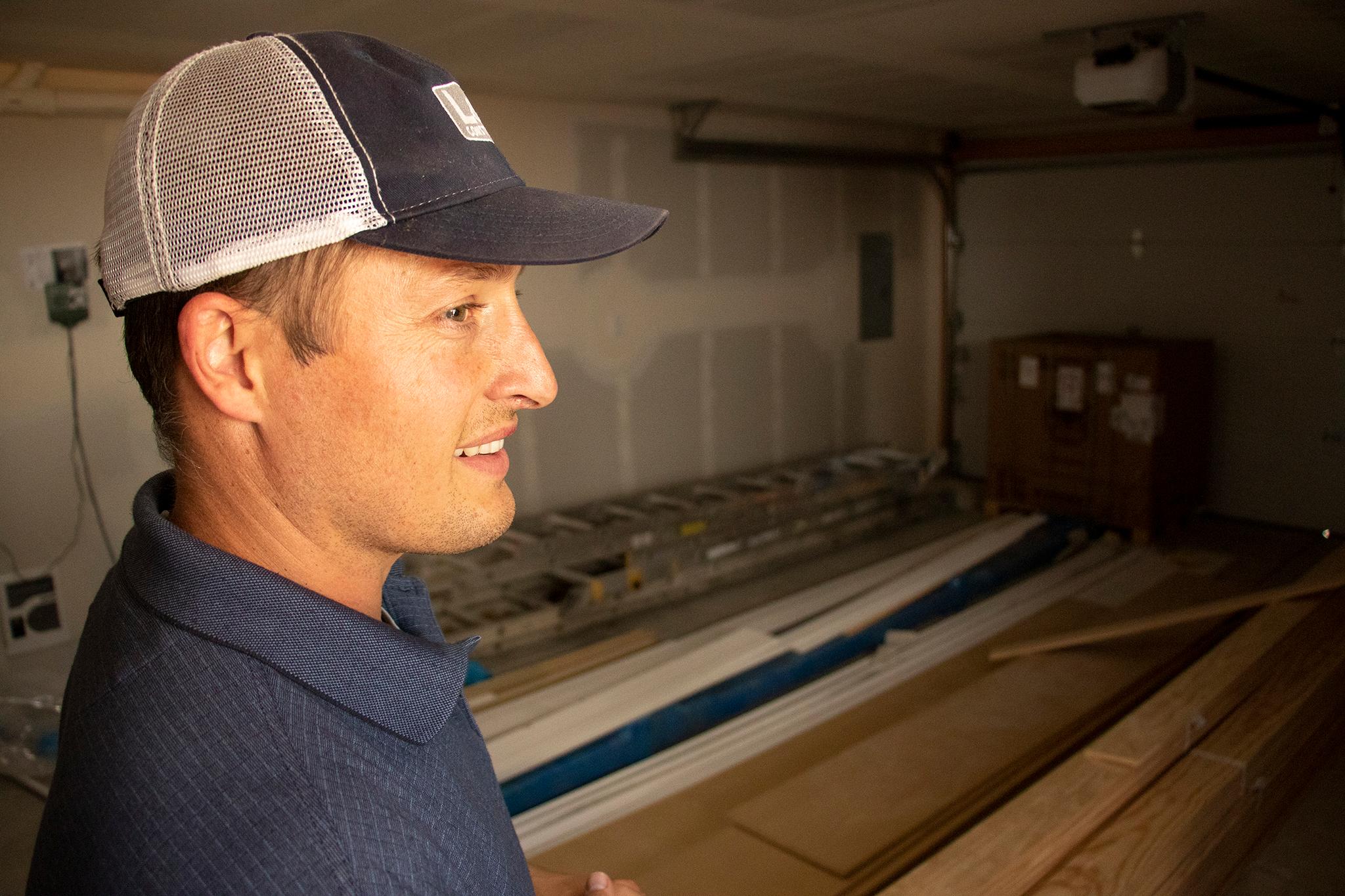
The McKinsey Global Institute has found that productivity among U.S. construction workers has been flat since 1945. Since then, the amount of work completed for every hour on the job increased as much as 1,500 percent for agriculture, manufacturing and retail workers who adopted new techniques. Robert Dietz, chief economist of the National Association of Homebuilders, said at a recent conference that modular and panel construction methods that could lower costs are used in only 4 percent of new American homes. Modular homes are shipped as three-dimensional boxes -- picture a room on a truck bed. In the Simple Homes's panelized technique, homes are shipped as flat pieces that are the assembled on site.
U.S. Department of Energy officials see modular home construction as one way to address productivity, affordability and other issues in the housing industry. The department in May issued a call to researchers to apply for millions of dollars in grants to develop modular and other construction techniques that address efficiency issues.
In Denver last month developers, contractors, Denver Housing Authority staff and others came out to gawk as a modular multifamily project using parts shipped from Idaho's Nashua Builders was assembled on a lot opposite Bronco's stadium for developer Rob Hahn. Colorado had pre-fab factories of its own before the great recession took its toll on the construction industry. Simple Homes's Schultz said launching a factory is capital intensive. The Colorado Economic Development Commission is considering incentives to help a nonprofit with which Simple Homes is not associated establish a prefab manufacturing factory in Colorado.
Erica Weeks, executive director of Habitat for Humanity of the San Juans, is intrigued at the faster, cheaper possibilities of the Simple Homes proposition.
"There's a high need for affordable housing in Colorado," she said. "How can we scale ourselves to meet that need?"
Weeks was in the early stages of studying the possibility of a pilot project with Simple Homes or perhaps another prefab builder. Among other considerations was how prefab construction would fit into her nonprofit's model, which relies on volunteer labor to help keep costs down. She said she was still learning about possible pitfalls of working with Simple Homes.
"Perhaps there aren't any and it does make sense," Weeks said.
Simple Homes's Hopfenbeck said addressing the affordability crisis helped drive the decision to start the company.
"Figuring out how to build houses more efficiently is a key part of solving the problem," he said.
Corrects to reflect that the modular technique is not the same as the Simple Homes panelized construction technique.