It was a home in two 11-by-65-foot boxes, wrapped in insulation and complete with windows, painted drywall, kitchen appliances, tub and toilet when it arrived on the back of a truck.
Then a crane lifted the boxes to be slotted into their places in what will be a four-story complex of up to 49 apartments at 1775 Federal Blvd., across from the Broncos stadium. The sight of a modular multifamily project going up in Denver was so rare that it drew a crowd of onlookers from Denver's housing and building community Tuesday.
"The overall process is a lot like building with Legos," said the West Colfax project's architect, Matt Chiodini of OZ.
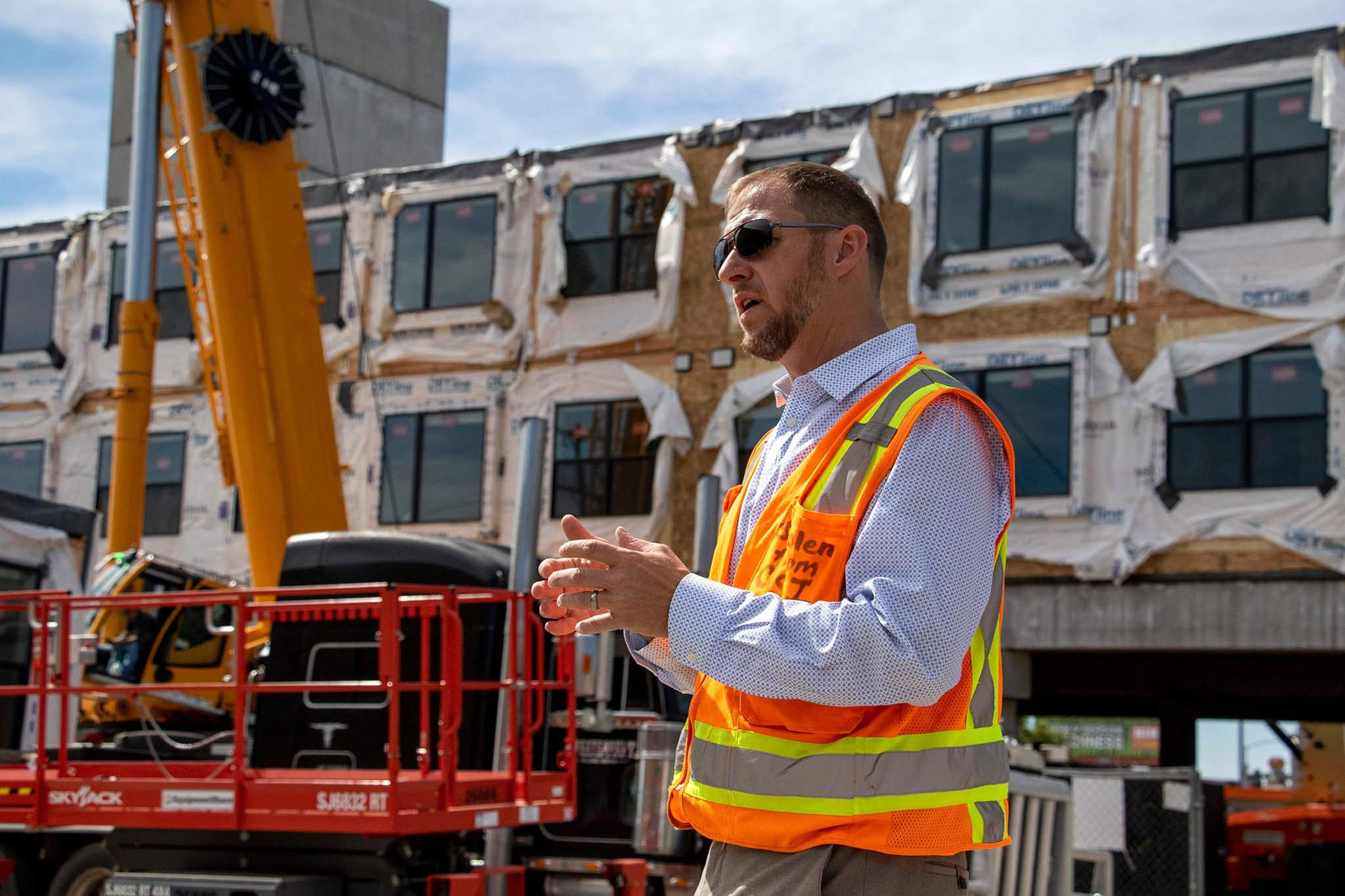

Chiodini told the assembled developers, contractors, Denver Housing Authority staff and others that the apartments, which may be sold as condos, were constructed at Nashua Builders's 250,000-square-foot factory in Boise, Idaho. Detroit-based general contractor Paul Gilbert was brought in to oversee the project. Gilbert has worked on modular projects around the country and with Nashua as well as other modular component suppliers such as Champion and Guerdon.
Modular construction is not new. But it is gaining new attention as one possible solution to a national housing shortage.
"This brings it to market faster," Chiodini said.
In its latest report on the state of U.S. housing, Harvard's Joint Center for Housing Studies concluded that a persistent "shortfall in new homes is keeping the pressure on house prices and rents, eroding affordability -- particularly for modest-income households in high-cost markets."
Among possible reasons for a relative lack of smaller, more affordable new homes restrictions, the Harvard researchers cited restrictions "on the supply of land available for higher-density development, regulatory constraints and not-in-my-backyard (NIMBY) opposition." Modular construction can't do much to address those factors, but the researchers also cited rising construction costs.
Rob Hahn, 1775 Federal's developer, said the modular route saved about 20 percent in construction costs.
Hahn has been developing infill projects in Denver for 15 years. He said he was "always looking for a better way."
He took a traditional construction approach on buildings like Avanti Food & Beverage, a Highland food hall. He also developed a 40-unit modular building elsewhere in Highland.
Not all sites are suitable for the crane needed to erect a modular building. When the site is right, a modular building can go up quickly. Architect Chiodini said building 1775 Federal conventionally would have taken 12 to 14 months. It is a six-to-eight-month modular project, he said. Anyone who has had to put up with a construction project in the neighborhood -- and that's a lot of anyones in Denver -- would surely appreciate that time frame.
"The cost saving comes in time," Hahn said.
"The biggest challenge in Denver right now is manpower," Hahn added.
Shain Zenor, Nashua's general manager, said his assembly line workforce of 150 can produce a unit in eight days. They can work year-round because they are working inside. Nashua completed all the units for 1775 Federal in four and a half weeks.
"We have a product we obviously want to sell," Zenor said. "If it's solving a need here, it's mutually beneficial."


OZ's Chiodini has toured a completed modular building in Seattle. Other examples include the 21-story citizenM, a Manhattan hotel completed last year with modular units shipped from Poland.
"Once you get inside these, you won't be able to discern whether or not this was built in a factory or was built conventionally," Chiodini said.
Crews began preparing the 1775 Federal site in January. That included erecting a prefab concrete podium on which the modular units are being placed. Weather delays and trouble finding construction workers in Denver put the project slightly behind schedule, Chiodini said.
The modular units each took a day and a half to be trucked from Boise to Thornton, where they first sat to acclimate.
On site Tuesday, it took eight minutes for the crane to place a unit. That process had begun a day earlier and was expected to take a week.
The final touches include an exterior facade.
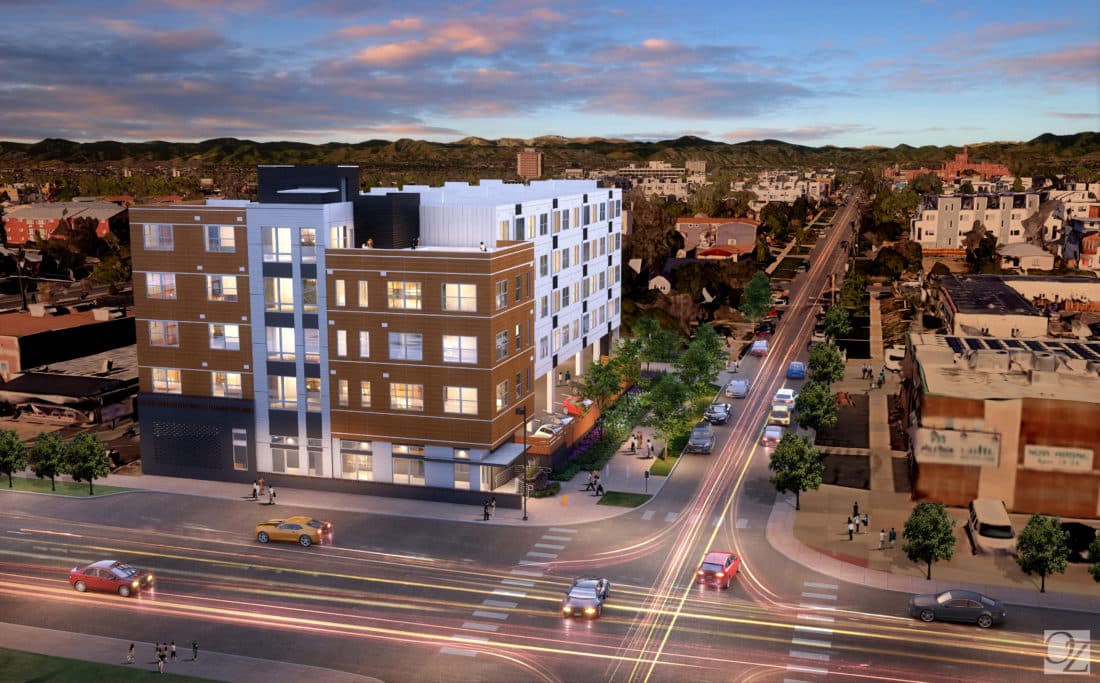